Монтаж сферических роликовых подшипников
с коническим отверстием
Содержание
1. Монтаж подшипников
2. Измерение величины уменьшения зазора
3. Измерение угла, на который затягивается стопорная гайка
4. Измерение осевого смещения
5. Измерение величины, на которую расширяется внутреннее
кольцо
6. Полезные ссылки
Монтаж подшипников
Натяг при установке на вал – обязательное характерное условие для подшипников, имеющих коническое отверстие. В качестве меры степени натяга используют величину смещения внутреннего кольца в осевом направлении на коническом месте установки либо его смещения в радиальном направлении. Ниже приведены методы контроля установки сферических роликоподшипников, оснащенных коническими отверстиями: измерение уменьшения зазора в роликоподшипнике; измерение угла, на который затягиваются стопорные гайки; измерение перемещения роликоподшипника вдоль оси вала; измерение величина, на которую растягивается внутреннее кольцо. Если подшипник имеет отверстие, диаметр которого менее 100 мм, то его правильная установка может быть осуществлена посредством замера угла, на который затянута стопорная гайка. Что же касается больших подшипников, то для них компания SKF разработала метод смещения, который и рекомендуется использовать. В отличие от метода замера угла, на который затянуты стопорные гайки и измерения величина на которую уменьшился радиальный зазор, метод смещения отличается более высокой точностью и требует минимальных временных затрат. Метод Sensor-Mount® позволяет измерить величину, на которую расширилось внутреннее кольцо. Ввиду того, что во внутреннем кольце подшипника находится соответствующий датчик, последний вышеупомянутый метод позволяет максимально быстро и точно установить подшипник.
Измерение величины уменьшения зазора
Нижеописанный метод характерен для больших и средних размеров подшипников, которые еще не установлены, либо уже демонтированы. Данный метод позволяет измерить внутренний радиальный зазор путем применения специального щупа. Как правило, зазор меряется между роликом, который не находится под нагрузкой, и наружным кольцом подшипника, как это показано на рисунке 14.
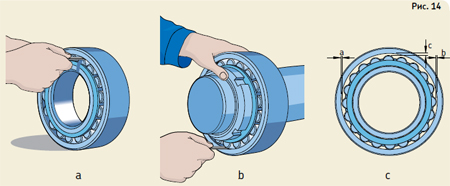
Многоразовая проверка внутреннего либо наружного кольца подшипника, предшествующая измерению, обязательна. Это необходимо для того, чтобы убедиться в относительной отцентровке обоих колец подшипника, а также комплекта подшипника. Чтобы провести первичное измерение, необходим щуп, толщиною чуть меньше, чем минимальный зазор. Введение щупа осуществляется возвратно-поступательными движениями, пока он не займет положение между роликом и дорожкой качения. Процедура повторяется необходимое количество раз с применением щупов различной толщины, пока вращению подшипника не будет оказано существенное сопротивление. Такое сопротивление создается:
- перед установкой подшипника, между верхним роликом и наружным кольцом, как показано на рисунке 14(а);
- после установки подшипника, между нижним роликом и наружным кольцом, как показано на рисунке 14(b).
Если измерение величины уменьшения зазора осуществляется для крупногабаритных подшипников, то за счет их массы либо усилия, которое создается, при введении между ненагруженными роликами и дорожкой качения, может возникнуть упругая деформация колец, что приводит к снижению точности измерений, особенно это характерно для подшипников, имеющих тонкие наружные кольца.
На рисунке 14(с) изображена процедура, характерная для выявления действительного зазора в таком случае. Способ применяется до либо после установки подшипника, а его этапы описаны ниже:
Если подшипник расположен на шейке вала, то его зазор «с»
меряется в положении 6 часов. Для стоящего подшипника замер
осуществляется в положении 12 часов.
Затем, в положении 9 часов меряется зазор «а», а потом, при
неизменном положении подшипника, в положении 3 часа, меряется
зазор «b».
Действительный внутренний зазор в радиальном направлении может
быть вычислен по формуле 0,5(a+b+c). Результат получается
достаточно точный.
В таблице 6 указаны послемонтажные размеры минимально
допустимого зазора, которые являются рекомендуемыми.
Измерение угла, на который затягивается стопорная гайка
На рисунке 15 показан простой способ правильной установки
средних и малых подшипников, имеющих коническое отверстие.
Данный метод контролирует угол, на который затягиваются
стопорные гайки. В таблице 6 указаны рекомендуемые размеры углов
затяжки стопорных гаек. Окончательной затяжке гаек должна
предшествовать установка подшипника на втулку либо коническое
посадочное место. Причем посадочная поверхность конического
внутреннего кольца средних и малых подшипников должна полностью
контактировать с посадочной поверхностью. Необходимый натяг
достигается путем поворота гайки на необходимый угол. Путем
поворотов наружного кольца и его вращения, можно проверить
остаточный зазор.
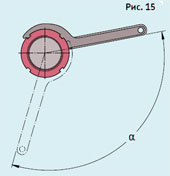
После этого необходимо снять гайку, поставить стопорную шайбу, а
затем снова затянуть гайку. Контровка гайки осуществляется после
затяжки загибом лапки стопорной шайбы в какой-либо паз гайки.
Если применяются гайки типа КМ, то ее необходимо сначала
вывернуть, поставить стопорную шайбу, после чего производится
повторная затяжка гайки.
Если применяются гайки типа KMFE, то для их фиксации нужно
затянуть установочный винт, при этом соблюдая моменты,
рекомендованные компанией SKF.
Измерение осевого смещения
Возможен вариант установки подшипников, имеющих коническое отверстие посредством измерения смещения внутреннего кольца относительно оси посадочного места. В таблице 6 указаны размеры осевого смещения, рекомендуемые компанией SKF.
Диаметр отверстия подшипника, мм | Уменьшение внутреннего радиального зазора, мм | Осевое смещение s1, мм | Допустимый остаточный2 радиальный внутренний зазор после монтажа гайки подшипника с начальным зазором | Угол затяжки α стопорной гайки | |||||||
d | Конусность 1:12 | Конусность 1:30 | Конусность 1:12 | ||||||||
более | включая | мин | макс | мин | макс | мин | макс | Нормальный | C3 | C4 | |
24 | 30 | 0,015 | 0,020 | 0,3 | 0,35 | - | - | 0,015 | 0,020 | 0,035 | 110 |
30 | 40 | 0,020 | 0,025 | 0,35 | 0,4 | - | - | 0,015 | 0,025 | 0,040 | 120 |
40 | 50 | 0,025 | 0,030 | 0,4 | 0,45 | - | - | 0,020 | 0,030 | 0,050 | 130 |
50 | 65 | 0,030 | 0,040 | 0,45 | 0,6 | - | - | 0,025 | 0,035 | 0,055 | 110 |
65 | 80 | 0,040 | 0,050 | 0,6 | 0,7 | - | - | 0,025 | 0,040 | 0,070 | 130 |
80 | 100 | 0,045 | 0,060 | 0,7 | 0,9 | - | - | 0,035 | 0,050 | 0,080 | 150 |
100 | 120 | 0,050 | 0,070 | 0,75 | 1,1 | 1,9 | 2,7 | 0,050 | 0,065 | 0,100 | - |
120 | 140 | 0,065 | 0,090 | 1,1 | 1,4 | 2,7 | 3,5 | 0,055 | 0,080 | 0,110 | - |
140 | 160 | 0,075 | 0,100 | 1,2 | 1,6 | 3,0 | 4,0 | 0,055 | 0,090 | 0,130 | - |
160 | 180 | 0,080 | 0,110 | 1,3 | 1,7 | 3,2 | 4,2 | 0,060 | 0,100 | 0,150 | - |
180 | 200 | 0,090 | 0,130 | 1,4 | 2 | 3,5 | 5 | 0,070 | 0,100 | 0,160 | - |
200 | 225 | 0,100 | 0,140 | 1,6 | 2,2 | 4 | 5,5 | 0,080 | 0,120 | 0,180 | - |
225 | 250 | 0,110 | 0,150 | 1,7 | 2,4 | 4,2 | 6 | 0,090 | 0,130 | 0,200 | - |
250 | 280 | 0,120 | 0,170 | 1,9 | 2,7 | 4,7 | 6,7 | 0,100 | 0,140 | 0,220 | - |
280 | 315 | 0,130 | 0,190 | 2 | 3 | 5 | 7,5 | 0,110 | 0,150 | 0,240 | - |
315 | 355 | 0,150 | 0,210 | 2,4 | 3,3 | 6 | 8,2 | 0,120 | 0,170 | 0,260 | - |
355 | 400 | 0,170 | 0,230 | 2,6 | 3,6 | 6,5 | 9 | 0,130 | 0,190 | 0,290 | - |
400 | 450 | 0,200 | 0,260 | 3,1 | 4 | 7,7 | 10 | 0,130 | 0,200 | 0,310 | - |
450 | 500 | 0,210 | 0,280 | 3,3 | 4,4 | 8,2 | 11 | 0,160 | 0,230 | 0,350 | - |
500 | 560 | 0,240 | 0,320 | 3,7 | 5 | 9,2 | 12,5 | 0,170 | 0,250 | 0,360 | - |
560 | 630 | 0,260 | 0,350 | 4 | 5,4 | 10 | 13,5 | 0,200 | 0,290 | 0,410 | - |
630 | 710 | 0,300 | 0,400 | 4,6 | 6,2 | 11,5 | 15,5 | 0,210 | 0,310 | 0,450 | - |
710 | 800 | 0,340 | 0,450 | 5,3 | 7 | 13,3 | 17,5 | 0,230 | 0,350 | 0,510 | - |
800 | 900 | 0,370 | 0,500 | 5,7 | 7,8 | 14,3 | 19,5 | 0,270 | 0,390 | 0,570 | - |
900 | 1000 | 0,410 | 0,550 | 6,3 | 8,5 | 15,8 | 21 | 0,300 | 0,430 | 0,640 | - |
1000 | 1120 | 0,450 | 0,600 | 6,8 | 9 | 17 | 23 | 0,320 | 0,480 | 0,700 | - |
1120 | 1250 | 0,490 | 0,650 | 7,4 | 9,8 | 18,5 | 25 | 0,340 | 0,540 | 0,770 | - |
1250 | 1400 | 0,550 | 0,720 | 8,3 | 10,8 | 21 | 27 | 0,360 | 0,590 | 0,840 | - |
1400 | 1600 | 0,600 | 0,800 | 9,1 | 11,9 | 22,7 | 29,8 | 0,400 | 0,650 | 0,920 | - |
1600 | 1800 | 0,670 | 0,900 | 10,2 | 13,4 | 25,4 | 33,6 | 0,440 | 0,720 | 1,020 | - |
1 - Действительно только для сплошных
стальных валов и общего применения. Не действительно при
использовании метода смещения SKF 2 - Величина остаточного зазора должна проверяться в тех случаях, когда величина начального радиального внутреннего зазора находится в нижней половине поля зазора и когда в процессе эксплуатации возникает большая разница температур между кольцами подшипника. Величина остаточного зазора должна превышать минимальные величины, указанные выше. |
Также компания SKF разработала собственный «точный метод монтажа», применяемый для таких целей. Данный метод прост и надежен, он позволяет довольно просто определить начальное расположение подшипника. Данное место и является исходной точкой при определении осевого смещения.
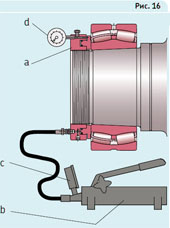
На рисунке 16 изображен монтажный инструмент, применяемый в этих
целях.
а – гайка SKF, гидравлическая, тип HMV..E;
b – насос гидравлический;
c – манометр, который рассчитан на условия установки;
d – индикатор.
Последовательно данный метод можно описать так:
1. На посадочном месте осуществляется предварительный монтаж
подшипника. Причем начальное положение можно определить по
давлению, создаваемому маслом в гидравлической гайке. На рисунке
17 показано, как может варьироваться давление.
2. При помощи гидрогайки осуществляется перемещение подшипника
на заранее известную величину – в его конечное положение. На
гидравлической гайке расположен индикатор часового типа, который
поможет определить точную величину перемещения Ss.
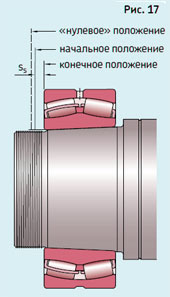
На рисунке 18 приведены схемы подшипниковых узлов, для которых
характерны значения осевого смещения и начального давления масла
в гидрогайке, которые заранее определены специалистами компании
SKF.
На рисунке 18(а) и 18(b) показана схема, для которой характерна
одна скользящая поверхность;
На рисунке 18(с) показана схема, для которой характерны две
скользящие поверхности.
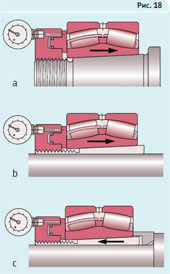
Измерение величины, на которую расширяется внутреннее кольцо
Крупногабаритные сферические подшипники, имеющие конические отверстия, могут быть легко и быстро установлены с помощью метода замера величина, на которую расширяется внутреннее кольцо. Вышеупомянутый метод не требует замера радиального зазора до установки и после нее. Метод установки SensorMount, разработанный компанией SKF, требует внедрение во внутреннее кольцо подшипника специального датчика, который контролируется соответствующим индикаторным прибором переносного типа. Структурная схема осуществления данного метода приведена на рисунке 19.
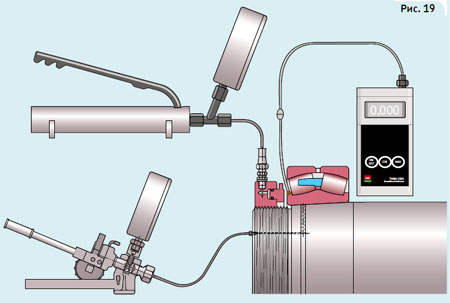
Установка подшипника на посадочное место конической формы осуществляется посредством применения стандартного монтажного инструмента, также разработанного компанией SKF. Специальный индикаторный прибор обрабатывает данные, которые поступают от датчика. Отношение уменьшения зазора, измеряемое в миллиметрах, к диаметру отверстия подшипника, измеряемого в метрах, говорит о том, насколько расширилось внутреннее кольцо и данная величина отображается на индикаторе.
При этом, цельная либо сплошная конструкция и материал вала, а также гладкость поверхности и размер подшипника не принимаются во внимание. В технической службе компании SKF, по Вашему запросу, будут представлены более подробные сведения относительно метода установки SensorMount, разработанного компанией SKF.
Полезные ссылки
Карта раздела
Сферические подшипники
Стандартные подшипники
Подшипники класса SKF Explorer
Специальные подшипники
Подшипники на втулках
Корпуса подшипников
Подшипники - основные сведения
Монтаж подшипников с коническим отверстием
Сферические роликовые подшипники в интернет-магазине